Paul’s Rubbish Removal and Demolition are evolving faster than many realize. From manual labor to advanced systems, the change is visible. This shift isn’t just about debris but also responsibility. Cleaner methods are becoming the standard.
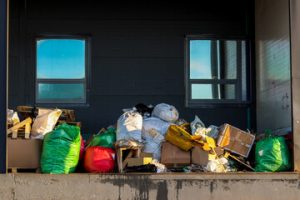
Most demolition jobs used to rely on brute force alone. Now precision tools reduce structural risk. This change minimizes waste and improves safety. It also opens new ideas on material salvage.
Material salvage is now treated as a resource stream. Instead of dumping, experts sort reusable elements. Bricks, metals, and timber get second lives. The value is no longer only in destruction.
Digital scanning has entered the demolition scene. It maps internal structures in seconds. Knowing where wires and pipes lie is vital. It prevents accidents and improves workflow efficiency.
Smart technology tracks debris movement in real-time. Load sensors calculate disposal weights instantly. Data records make reporting and regulation easier. Tracking is part of today’s cleanup protocol.
Dust suppression is another emerging focus. Older sites were clouds of toxic dust. Now fine mist sprays neutralize airborne hazards. Air quality matters even in temporary zones.
Noise control has also improved dramatically. Hydraulic crushers replaced traditional hammers. Worksites are now less disruptive to neighbors. This change makes demolition less intrusive.
Selective deconstruction is a rising trend. It prioritizes careful removal over complete collapse. Each material is removed strategically. This results in greater savings and reuse potential.
Waste audits are now standard before large jobs. Planners assess the likely waste stream. This helps tailor the removal strategy early. Fewer surprises lead to smoother project timelines.
Some companies use AI for sorting debris. Cameras distinguish materials at incredible speeds. This cuts sorting time by a huge margin. It’s waste handling with machine vision.
Energy recovery from waste is becoming popular. Certain rubbish materials can fuel turbines. Instead of landfill, energy gets harvested. This dual-purpose model reduces carbon footprints.
Hybrid demolition machinery is now available. These use electric and fuel systems together. Quieter and cleaner, they suit urban environments. Many are remote-controlled for added safety.
The layout of a site impacts removal efficiency. Experts map traffic flows before work begins. This prevents clogs and delays in hauling. Logistics are as vital as manpower.
Salvage resale markets are thriving quietly. Reclaimed wood and vintage brick are in demand. What was trash becomes architectural gold. This shift alters how we define value.
Demolition teams now collaborate with recycling experts. Coordinated plans ensure maximum waste recovery. This minimizes landfill reliance. Collaboration replaces the siloed work model.
Micro-demolition is gaining popularity in urban zones. It breaks down interiors without full teardown. Offices, kitchens, and bathrooms get reworked surgically. This is ideal for tenants and remodelers.
3D modeling helps forecast demolition phases. Managers use simulations to predict outcomes. Delays and conflicts are identified in advance. This improves efficiency and cost control.
Some projects now require waste-neutral outcomes. All waste must be accounted for and redirected. No materials go to uncontrolled dumps. Accountability adds to credibility and compliance.
Drone surveillance boosts site safety daily. Drones capture real-time footage from above. Supervisors spot risks without setting foot inside. It’s oversight without physical intrusion.
Demolition isn’t just physical anymore. Administrative layers ensure environmental compliance. Licenses, reports, and audits are all tracked. Paperwork equals protection against future liability.
Asbestos handling is now tightly regulated. Specialists isolate and remove it with care. Full-body suits and sealed containers are required. Mishandling leads to health and legal issues.
Lead paint detection is part of every old structure check. If found, proper containment follows. Safe scraping and vacuum tools reduce dust. Workers undergo specialized training.
Recyclable debris piles are tagged and tracked. Each item type has a different route. Plastics, concrete, glass, and metals are sorted. The chain of custody matters now.
Eco-certifications add credibility to demolition contractors. Green compliance boosts client confidence. It can also qualify projects for incentives. Certification is no longer optional for many.
Underground sensors help detect unknown pipes. These systems prevent utility disruption. Digging becomes safer and faster. Tech continues to prevent common site issues.
Robot-assisted demolition helps reduce physical strain. These machines operate where humans can’t. Narrow corridors and fragile floors benefit most. It’s safer and more precise.
Interior demolition now includes selective protection zones. Some rooms are left untouched. Barriers shield them from dust and debris. Careful planning prevents unintentional damage.
Concrete recycling is a game-changer in urban areas. Crushers grind slabs into reusable aggregate. This cuts both waste and material costs. It’s efficient and environmentally sound.
Steel frames are carefully torched and reused. Metal beams retain their strength for future builds. Melting and reforming isn’t always necessary. Direct reuse skips energy-intensive processes.
Roof removal follows new eco-guidelines too. Tar and shingle separation is now common. Recyclable shingles are ground into pavement. Less roof waste reaches landfill sites.
Jobsite debris is no longer just tossed in dumpsters. Collection bins are now sorted by color. Workers get trained in proper separation. It’s organization over chaos.
Old drywall is now processed into soil conditioner. Gypsum improves soil structure and water balance. Agricultural sectors benefit from construction waste. Circular solutions emerge from demolition work.
Insulation materials require special handling now. Fiberglass and foam can’t just be burned. Certain types are bagged and sent for melting. Others get repurposed in acoustic panels.
Brick recovery includes on-site cleaning systems. Machines scrub bricks without damaging them. This saves manual labor and increases reuse. Bricks retain their aged charm.
Landfill alternatives are expanding across regions. Some use industrial composting for organic debris. Others apply anaerobic digestion techniques. New models outpace traditional dumping.
Glass panels and windows are now carefully removed. Once shattered, glass becomes harder to recycle. Removing intact saves both time and energy. Some get reused in art or architecture.
Old furniture from demolition is reclaimed creatively. Broken wood becomes rustic tables. Iron legs are repurposed into home accents. This is demolition with an artistic edge.
Painted surfaces are now checked for toxic content. Stripping must follow safety protocol. Workers wear masks and use filtered vacuums. Safe removal is prioritized over speed.
Rubber floor tiles are ground into playground padding. The texture absorbs impact from falls. Kids benefit from recycled construction waste. Everyone wins when reuse is the goal.
PVC pipes can be cleaned and reshaped. Some go into fencing, others into signage. Demolition no longer ends in material loss. It’s a pipeline to second lives.
Power tools used today reduce environmental harm. Battery-powered equipment has replaced gas engines. Quieter, cleaner, and equally strong. Technology reshapes every worker’s toolkit.
Fire-damaged buildings require unique removal steps. Ash, soot, and chemical hazards are isolated. Cleanup follows hazardous material protocol. Speed never outweighs safety.
The future of rubbish removal looks more modular. Tiny units manage waste room-by-room. These mobile stations pre-sort materials. Decentralized cleanup is more efficient.
Community programs now accept leftover demolition materials. Residents repurpose doors, frames, and tiles. These donations reduce waste and foster community pride. Sharing is a new form of disposal.
Education on responsible demolition starts in trade schools. Students learn salvage and eco-compliance early. These lessons create skilled, mindful workers. Training builds both safety and sustainability.
Demolition documentaries are raising awareness. People now see the value of clean destruction. It’s no longer just smashing and tossing. Minds are shifting toward mindful teardown.
Some contractors experiment with biodegradable barriers. Instead of plastic tarps, plant-based nets are used. These decompose after the job ends. Less waste, same performance.
Artificial intelligence predicts demolition timelines. Software adjusts daily based on performance. This ensures deadlines are met safely. Smart systems save time and money.
Even scheduling has become eco-conscious. Off-peak hours reduce city congestion. Less traffic means fewer emissions. Every detail now considers environmental cost.
Future demolition might be zero-emission entirely. Solar-powered machines are being tested. Charging stations are built into site plans. Clean energy meets clean removal.
The industry has begun seeing rubbish as potential. What was waste now fuels innovation. Demolition is becoming circular, not linear. It’s a quiet revolution from the ground up.