Many types of plastic can be ultrasonically welded. In most situations the two parts to be welded must be made of the same type of plastic.
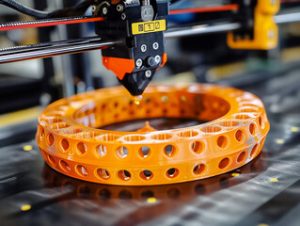
Chemical compatibility is determined by Melt Flow Index (MFI) values. For best results, it is preferred that both materials have similar MFIs. After a predetermined time or distance, the weld process is stopped and the plastics cool down to form a strong bond. Read on Ultrasonic Plastic Welding Machines Florida for more information.
1. Easy to Operate
Ultrasonic Plastic Welding Machines utilize the mechanical energy of vibration to join two or more pieces of plastic together. The vibrations are generated by a sonotrode or other device, which is designed specifically for the type of work being done. The vibrations travel through the sonotrode and are reflected back into it, which creates heat friction at the contact surface between the two parts. This heat causes the plastic to melt, forming a bond between the materials. The resulting weld is strong and clean. The process is also much faster than traditional welding methods, with most welds taking less than three seconds.
In addition, sonic plastic welding machines require no preheating, which means they can operate at high speeds that are suitable for mass production. They are also easy to maintain, with minimal energy consumption and no need for expensive compressed air systems.
The process is effective on a wide variety of plastics, although some are easier to weld than others. The best plastics for ultrasound welding are those with a more amorphous structure, which is easy to fuse using sonic energy. Examples include polyethylene and acrylonitrile butadiene styrene (ABS). Parts with a more crystalline structure, such as polyvinyl chloride (PVC) or cellulose acetate butyrate (CA/B/P), are typically difficult to weld with ultrasound. When choosing a plastic for ultrasonic welding, consider its Tg, chemical compatibility, and Melt Flow Index (MFI)—all of which are important factors when gauging weldability between dissimilar plastics.
Unlike conventional plastic welding techniques, the weld produced by an ultrasonic machine is hermetic and very clean. This makes it ideal for food applications that need a hermetic seal, such as dairy products like milk and juice containers. The sanitary nature of this technique also allows it to be used on paper components, such as candy bar wrappers or frozen food packages.
Dukane has a complete line of sonic welding equipment, including microprocessor-controlled plastic welders, remote actuators, kits for automation, and power supplies. They are available in a range of frequencies, from the industry standard at 20 kHz to the latest servo technology that uses 35 kHz for higher accuracy and superior results.
2. Economical
The ultrasonic plastic welding process eliminates the need for adhesives, which saves on production costs and helps meet environmental goals. It also produces strong and hermetic seals, making it ideal for manufacturing medical devices.
The key to successful and repeatable ultrasonic plastic welding is proper maintenance. Daily maintenance tasks include cleaning, lubricating and tightening loose fasteners. This ensures that the equipment functions as designed, delivering optimal performance and extending service life. It also prevents costly downtime and repairs.
Ultrasonic plastic welding is a versatile technology suitable for many industries and applications. It’s particularly useful in manufacturing medical products because it doesn’t introduce contaminants and allows for strict control of dimensional tolerances.
In addition, it increases productivity without sacrificing quality and helps to meet regulatory requirements by eliminating the need for hazardous chemicals. It’s also a great choice for food production because it creates durable, hermetic seals that prevent contamination and spoilage.
To create an ultrasonic weld, a generator converts 50-60Hz electricity into high-frequency vibration. This energy is transferred to the transducer, which then transmits the ultrasonic waves through a booster that amplifies them. The ultrasonic waves vibrate at 10’s of thousands of times per second and generate heat. The heat melts the upper and lower parts of the plastic assembly, which are then joined together at the welding point.
When selecting a plastic for an ultrasonic weld, consider its melting behavior and its glass transition temperature (Tg). It’s best to use thermoplastics that soften gradually over a wide range of temperatures. These materials have an amorphous structure and are the easiest to weld.
Another important factor is the acoustic impedance of the part to be weld. The higher the acoustic impedance, the more difficult it is to weld. To reduce the acoustic impedance, manufacturers may use a horn, a resonator, or an anvil to hold the parts. They can also adjust the welding parameters by changing the trigger force, amplitude, or time of exposure.
3. Environmentally Friendly
Welding using ultrasound is an environmentally friendly plastic welding process because it eliminates the need for harmful solvents to make a bond. This makes it ideal for medical devices, as it can be used to create sterile connections without sacrificing the strength of the components. Ultrasonic welding also requires less energy than other welding methods and is faster, which helps reduce manufacturing costs and waste.
To start the process, an electrical signal is transmitted from the machine’s generator to the power converter. This converts the electrical energy into mechanical vibrations that are transferred to a component called the “Booster.” The amplitude of these vibrations can be adjusted depending on the application of the weld to be made.
The welding horn or sonotrode is positioned between the two parts that need to be joined together and the converter and booster are activated. The vibrations travel through the welding rib positions and cause friction between them, which generates heat under pressure. The vibrations also create an electromagnetic field between the rib positions that acts to guide the energy to where it is needed in order to complete the weld.
One of the most significant advantages of Ultrasonic Plastic Welding Machines is that they are more effective than other plastic welding processes at joining dissimilar materials. This is because the welding method relies on a phenomenon known as “sonic energy directorship.” This allows the welder to focus the mechanical vibrations where they are needed in order to complete the weld, rather than having them spread out over a large area.
It is important to understand how this works in order to optimize the operation of an Ultrasonic Welding Machine. For example, it is best to use the welder for materials that have an amorphous structure and a melting behavior that is characterized by a glass transition temperature, or Tg. In addition, it is advisable to consider chemical compatibility and the melt flow index (MFI) of both the welder and the material being welded.
It is essential to keep your Ultrasonic Plastic Welding Machines in good working condition in order to avoid costly downtime and improve production efficiency. You should perform regular inspections and maintenance of the equipment to make sure it is functioning correctly. When repairs are required, it is recommended that you always consult a professional before performing any disassembly of the machine. This will ensure that you do not accidentally damage any internal components.
4. High-Quality Welds
Ultrasonic plastic welding produces clean, strong and reliable welds in milliseconds. It also avoids the use of heat-generating adhesives, which saves energy and money as well as eliminating the need for hazardous materials in your workflow. It is suitable for many applications and a wide range of polymer types, making it ideal for a broad range of industries.
RTUL Group’s Ultrasonic Plastic Welding Machines can help you get the best results out of this innovative process. To maximize its benefits, consider these tips for a successful application:
The Welding Process
Ultrasonic welding is an advanced bonding technique that works by binding plastic parts together through high-frequency vibrations. It can be used on a variety of polymers, including thermoplastics and thermosets. The key is to select materials that are similar in chemical composition and physical properties. This ensures that the molecular bonds created will be strong and stable.
In addition to choosing compatible materials, the type of weld you want will also influence the final result. Different welding modes use varying amounts of energy to create the welds, and some require a certain level of skill to achieve optimal results.
For the most precise control, an ultrasound system can be equipped with a programmable ultrasonic tool stack, allowing you to modify the frequency of the vibrations and their duration. This feature will allow you to create a specific amplitude for each weld type, ensuring that your welds are of the highest quality.
Another way to improve the weld quality is by using a shear joint. This welding method produces welds that are more resistant to shear and tensile stress, and is especially useful in joining dissimilar materials.
A shear joint is also a great choice for thin parts, as it can be achieved with less energy than the other two common weld modes. However, this mode is not recommended for thick parts, as the excessive amplitude could cause damage to the part.
In addition to offering a fast cycle time, sonic plastic welding can be highly repeatable, even with the same machine settings. For this reason, it is ideal for processes that need a high level of consistency. In addition, sonic welding can be performed without the need for an air compressor, eliminating the possibility of fluctuations in incoming air pressure.